Top-performing absorber materials for heat collector panels include black chrome coatings, selective cermet absorbers, and carbon nanotubes. These materials offer high solar absorptance and low thermal emittance, maximizing heat collection efficiency. Black chrome coatings provide excellent durability, while cermet absorbers excel in high-temperature applications. Carbon nanotubes offer exceptional thermal conductivity and light absorption. Other effective options include copper oxide surfaces, nickel-aluminum alloy coatings, and spectrally selective paints. Each material has unique properties that contribute to improved solar thermal system performance. Understanding these materials' characteristics can help you make informed decisions for your heat collector panel needs.
Black Chrome Coating
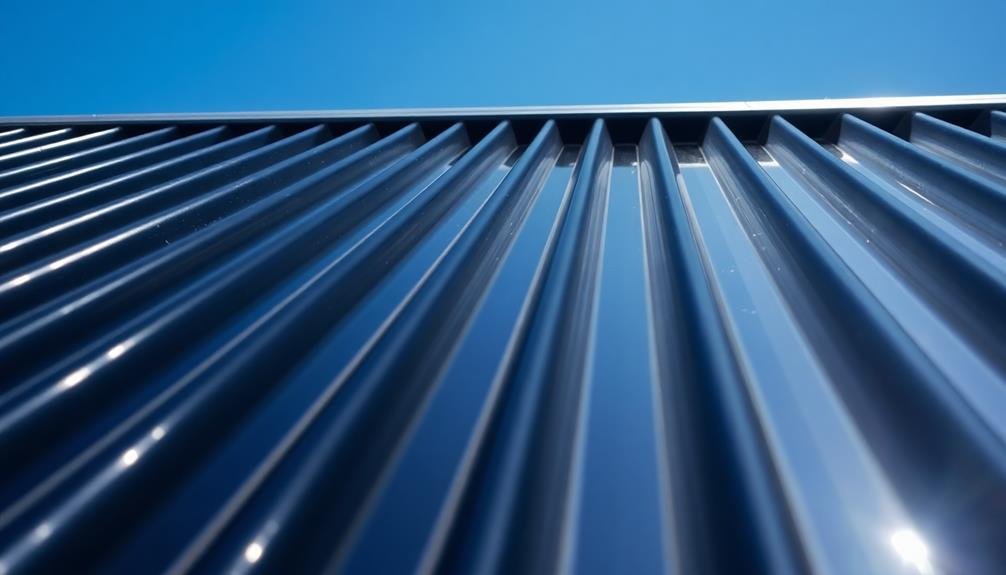
Black chrome's exceptional absorptive properties make it a top choice for heat collector panels. You'll find that this electroplated coating combines high solar absorption with low thermal emittance, maximizing energy capture. It's composed of tiny chromium particles suspended in a chromium oxide matrix, creating a selective surface that traps sunlight effectively.
When you're considering black chrome for your heat collector panels, you'll appreciate its durability and resistance to weathering. It maintains its performance over time, even in harsh outdoor conditions. You can expect absorption rates of up to 96% and emittance as low as 12%, resulting in excellent thermal efficiency.
The application process for black chrome involves electroplating onto a nickel-plated copper or aluminum substrate. You'll need to verify proper thickness and uniformity for peak performance. While it's more expensive than some alternatives, black chrome's longevity and efficiency often justify the investment.
You should be aware that black chrome contains hexavalent chromium, which poses environmental concerns. However, recent developments in trivalent chromium coatings offer a more eco-friendly alternative with similar performance characteristics.
When selecting black chrome, consider both its superior absorptive qualities and environmental impact.
Selective Cermet Absorbers
You'll find selective cermet absorbers composed of metal particles dispersed in a ceramic matrix, often combining materials like nickel, chromium, or molybdenum with alumina or silica.
These absorbers exhibit excellent solar absorption and low thermal emittance due to their unique composition and layered structure.
You can expect cermet absorbers to offer high thermal stability and durability, making them suitable for high-temperature solar thermal applications.
Composition and Structure
Selective cermet absorbers represent a cutting-edge solution in solar thermal technology. These advanced materials combine the best properties of ceramics and metals to create highly efficient absorber coatings. You'll find that cermets typically consist of metal nanoparticles dispersed within a ceramic matrix.
The composition of cermet absorbers usually includes metals like nickel, chromium, or molybdenum embedded in ceramic materials such as alumina, silica, or titanium nitride. This unique structure allows for excellent solar absorption while minimizing thermal emittance. The metal particles, often 5-50 nm in size, enhance light absorption, while the ceramic matrix provides durability and stability at high temperatures.
The structure of cermet absorbers is carefully engineered to optimize their performance. You'll see that they're often designed as multi-layer coatings, with each layer serving a specific purpose.
The top layer is typically antireflective, followed by the cermet layer, which absorbs solar radiation. A reflective metal layer at the bottom helps prevent infrared radiation loss. This layered structure allows you to achieve high solar absorptance (>95%) and low thermal emittance (<10%), resulting in superior efficiency for your heat collector panels.
Performance Characteristics
The performance characteristics of selective cermet absorbers stem directly from their unique composition and structure. You'll find that these materials excel in solar thermal applications due to their high solar absorptance and low thermal emittance. They're designed to maximize the absorption of solar radiation while minimizing heat loss through radiation.
Selective cermet absorbers typically achieve solar absorptance values above 0.95 and thermal emittance values below 0.1. This combination results in excellent photothermal conversion efficiency, allowing for higher operating temperatures and improved overall system performance.
Here's a comparison of key performance characteristics:
Characteristic | Cermet Absorbers | Black Paint | Electroplated Black Chrome |
---|---|---|---|
Solar Absorptance | >0.95 | 0.9-0.98 | 0.92-0.94 |
Thermal Emittance | <0.1 | 0.8-0.9 | 0.08-0.12 |
Durability | High | Low | Moderate |
Cost | Moderate-High | Low | Moderate |
You'll notice that cermet absorbers offer a superior balance of high absorptance and low emittance compared to other options. They're also highly durable, maintaining their performance over extended periods of high-temperature operation and thermal cycling. This makes them ideal for long-term use in solar thermal collectors, despite their higher initial cost.
Carbon Nanotubes

Carbon nanotubes represent a cutting-edge development in absorber materials for heat collector panels. These microscopic structures offer exceptional thermal conductivity and light absorption properties, making them highly efficient in converting solar energy to heat.
You'll find that carbon nanotubes can greatly enhance the performance of heat collector panels due to their unique characteristics.
When incorporated into absorber materials, carbon nanotubes provide several advantages:
- High thermal conductivity, allowing for rapid heat transfer
- Excellent light absorption across a wide spectrum
- Durability and resistance to environmental factors
- Potential for improved overall system efficiency
You can expect carbon nanotube-enhanced absorbers to outperform traditional materials in many aspects. They're capable of absorbing more sunlight and converting it to heat more efficiently, which translates to higher energy output for your heat collector panels.
Additionally, their durability means you'll likely see extended lifespans for your panels, reducing maintenance costs and improving long-term performance.
As research in this field progresses, you'll likely see more widespread adoption of carbon nanotube-based absorber materials in heat collector panels. This technology promises to revolutionize solar thermal energy systems, offering improved efficiency and cost-effectiveness for both residential and industrial applications.
Copper Oxide Surfaces
You'll find copper oxide surfaces to be highly efficient absorbers for heat collector panels, with absorption rates often exceeding 95%.
These surfaces exhibit excellent thermal stability, maintaining their performance even under prolonged exposure to high temperatures.
You can fabricate copper oxide surfaces through various methods, including thermal oxidation, chemical oxidation, and electrodeposition, each offering unique advantages regarding cost and scalability.
High Absorption Efficiency
When it comes to maximizing the efficiency of heat collector panels, copper oxide surfaces stand out as exceptional absorber materials. You'll find that these surfaces can achieve high absorption efficiency, typically absorbing over 95% of incident solar radiation. This remarkable performance is due to their unique optical properties and surface structure.
Copper oxide surfaces offer several advantages for heat collector panels:
- Broad spectral absorption range, covering most of the solar spectrum
- Low thermal emittance, reducing heat loss through radiation
- Excellent durability and resistance to environmental factors
- Cost-effective production methods, making them commercially viable
You'll notice that copper oxide surfaces often appear black or very dark, which contributes to their high absorption efficiency. This color is a result of the material's band gap structure and light-trapping surface features.
By utilizing advanced deposition techniques, you can create copper oxide surfaces with refined nanostructures that further enhance their absorption capabilities.
When designing heat collector panels, you should consider the thickness and composition of the copper oxide layer. Thicker layers generally provide better absorption, but they may also increase thermal resistance.
You'll need to strike a balance to achieve peak performance for your specific application.
Thermal Stability Characteristics
Copper oxide surfaces not only excel in absorption efficiency but also demonstrate impressive thermal stability characteristics. You'll find that these surfaces maintain their performance over extended periods of high-temperature exposure, making them ideal for long-term use in heat collector panels. The thermal stability of copper oxide is attributed to its strong chemical bonds and crystalline structure.
When you're considering absorber materials, it's essential to understand how they perform under various temperature conditions. Here's a breakdown of copper oxide's thermal stability characteristics:
Temperature (°C) | Stability Duration | Performance Retention |
---|---|---|
200-300 | >10,000 hours | 98-99% |
300-400 | >5,000 hours | 95-97% |
400-500 | >2,000 hours | 90-93% |
500-600 | >1,000 hours | 85-88% |
>600 | <500 hours | <80% |
As you can see, copper oxide surfaces maintain excellent stability up to 500°C, with minimal degradation in performance. This thermal resilience guarantees that your heat collector panels will operate efficiently for extended periods, reducing maintenance costs and improving overall system reliability. The material's ability to withstand high temperatures without significant structural changes or loss of absorption properties makes it a top choice for solar thermal applications.
Fabrication Methods
For the production of efficient copper oxide absorber surfaces, several fabrication methods have been developed. You'll find that these techniques aim to create a uniform, durable, and highly absorptive layer on copper substrates. The most common methods include chemical oxidation, thermal oxidation, and electrodeposition.
Chemical oxidation involves immersing copper sheets in oxidizing solutions, often containing alkaline compounds. You'll need to carefully control the solution concentration, temperature, and immersion time to achieve the desired oxide thickness and composition.
Thermal oxidation, on the other hand, requires heating copper in an oxygen-rich environment, allowing you to form oxide layers through direct reaction with atmospheric oxygen.
Electrodeposition is a more precise method, where you'll apply an electric current to deposit copper oxide directly onto the substrate. This technique offers excellent control over the oxide layer's thickness and composition.
When selecting a fabrication method, consider these factors:
- Desired oxide layer thickness and composition
- Production scale and cost-effectiveness
- Available equipment and expertise
- Environmental impact and waste management
Nickel-Aluminum Alloy Coatings

Nickel-aluminum alloy coatings have emerged as a promising absorber material for heat collector panels. These coatings offer excellent thermal properties and durability, making them ideal for solar thermal applications. You'll find that Ni-Al alloys can be tailored to achieve high solar absorptance and low thermal emittance, optimizing the efficiency of your heat collector panels.
When you're considering Ni-Al alloy coatings, you'll want to focus on their composition and deposition method. The table below highlights key aspects:
Composition | Deposition Method | Advantages |
---|---|---|
Ni3Al | Magnetron sputtering | High temperature stability |
NiAl | Electroplating | Cost-effective |
Ni2Al3 | Thermal spraying | Thick coatings |
You'll notice that each composition and deposition method offers unique benefits. For instance, Ni3Al coatings deposited by magnetron sputtering provide excellent high-temperature stability, essential for long-term performance. On the other hand, if you're looking for a more cost-effective option, NiAl coatings applied through electroplating might be your best bet. Remember, the choice of Ni-Al alloy coating will depend on your specific requirements and budget constraints.
Titanium Nitride Films
While nickel-aluminum alloys offer excellent performance, titanium nitride films have gained considerable attention in the field of heat collector panels. You'll find that these films provide a unique combination of properties that make them ideal for solar thermal applications.
Titanium nitride coatings are known for their high absorption in the visible spectrum and low emissivity in the infrared range, making them efficient at trapping and retaining heat.
When you're considering titanium nitride films for your heat collector panels, keep these key points in mind:
- They're extremely durable and resistant to wear, corrosion, and high temperatures
- You can apply them using various deposition techniques, including sputtering and chemical vapor deposition
- They exhibit excellent adhesion to various substrate materials
- Their optical properties can be fine-tuned by adjusting the film thickness and deposition parameters
You'll appreciate that titanium nitride films can considerably improve the overall efficiency of your heat collector panels.
They're particularly effective in high-temperature applications, where their stability and performance outshine many other absorber materials. By incorporating titanium nitride films into your design, you'll be able to create more efficient and long-lasting solar thermal systems.
Silicon-Based Absorbers
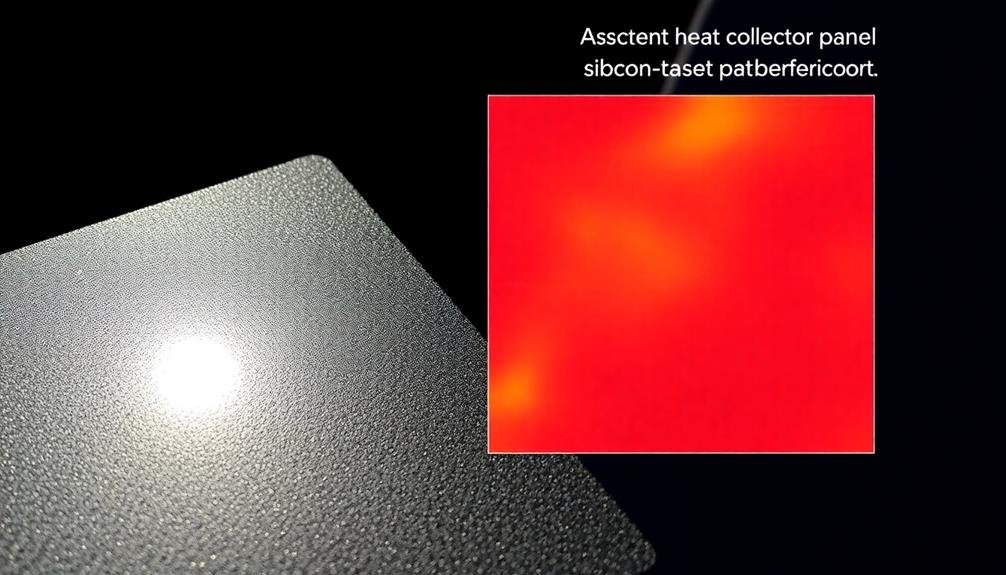
Silicon, the workhorse of the electronics industry, has found its way into solar thermal applications as a promising absorber material for heat collector panels.
You'll find that silicon-based absorbers offer several advantages, including high absorption in the visible spectrum and low emissivity in the infrared range.
One popular approach is using amorphous silicon (a-Si) coatings. These thin films can be deposited on various substrates, offering flexibility in design and manufacturing.
You can further enhance their performance by incorporating nanostructures or multilayer designs.
Another innovative solution is black silicon. This material features a nanostructured surface that traps light effectively, resulting in exceptionally high absorption rates.
You'll appreciate its potential for improving the efficiency of heat collector panels.
Silicon-germanium alloys have also shown promise. By adjusting the composition, you can fine-tune the optical properties to match specific requirements.
These alloys offer improved thermal stability compared to pure silicon.
When considering silicon-based absorbers, you should evaluate factors such as durability, cost-effectiveness, and scalability.
While they may not yet match the performance of some metal-based absorbers, ongoing research continues to narrow the gap, making silicon an increasingly viable option for heat collector panels.
Black Nickel Coatings
You'll find black nickel coatings to be highly effective absorbers with excellent absorption properties and low emissivity.
When applying these coatings, you need to evaluate their durability under varying temperatures and environmental conditions.
Their performance and longevity can be affected by factors such as humidity, UV exposure, and thermal cycling, so you'll want to assess these aspects carefully for your specific application.
Absorption and Emissivity Properties
Black nickel coatings have emerged as a popular choice for absorber materials in heat collector panels due to their exceptional absorption and emissivity properties. These coatings exhibit high solar absorption rates, typically above 0.95, while maintaining low thermal emissivity, usually below 0.07. This combination allows for efficient capture of solar energy while minimizing heat loss through radiation.
You'll find that black nickel coatings offer several advantages:
- High selectivity ratio (absorption to emissivity)
- Excellent durability and resistance to weathering
- Compatibility with various substrate materials
- Cost-effective production methods
When you're considering black nickel coatings for your heat collector panels, it's important to understand how their properties affect performance. The high absorption rate guarantees that most incoming solar radiation is captured, while the low emissivity reduces re-radiation of absorbed energy. This results in higher overall efficiency and improved heat retention within the collector.
You can further optimize the performance of black nickel coatings by adjusting their thickness and composition. Thicker coatings generally offer higher absorption rates but may also increase emissivity. By fine-tuning these parameters, you can achieve the ideal balance for your specific application, maximizing the efficiency of your heat collector panels.
Application and Durability Considerations
When applying black nickel coatings to heat collector panels, you'll need to take into account several factors to assure peak performance and longevity.
First, verify the substrate is thoroughly cleaned and prepared to promote strong adhesion. You'll want to use electroplating or electroless deposition techniques for uniform coating thickness, typically ranging from 0.2 to 1.0 micrometers.
Consider the operating temperature range of your heat collector panels, as black nickel coatings perform best up to 300°C. Beyond this temperature, you may experience degradation and reduced efficiency.
To enhance durability, you can apply a protective layer of silicon dioxide or aluminum oxide over the black nickel coating.
Be aware that black nickel coatings are susceptible to humidity and corrosive environments. You'll need to implement proper sealing and moisture barriers to prevent oxidation and maintain coating integrity.
Regular maintenance, including gentle cleaning with non-abrasive materials, will help prolong the coating's lifespan.
When selecting black nickel coatings, opt for those with high absorptivity (>0.95) and low emissivity (<0.10) to maximize heat collection efficiency.
You'll find that these coatings offer an excellent balance between performance and cost-effectiveness for most solar thermal applications.
Graphene-Enhanced Materials

One of the most promising advancements in absorber materials for heat collector panels is the incorporation of graphene. This revolutionary nanomaterial has exceptional thermal conductivity and optical properties, making it an ideal candidate for enhancing the performance of solar thermal systems.
When you're looking to improve your heat collector panels, graphene-enhanced materials offer several advantages.
Graphene's unique structure allows it to efficiently absorb and transfer heat, considerably boosting the overall efficiency of your solar thermal system.
You'll find that these materials can:
- Increase thermal conductivity by up to 25%
- Enhance light absorption across a broader spectrum
- Improve durability and resistance to thermal degradation
- Reduce the overall weight of the absorber material
Aluminum Nitride Composites
Aluminum nitride composites represent another cutting-edge development in absorber materials for heat collector panels. These innovative materials combine the exceptional thermal conductivity of aluminum nitride with other components to create highly efficient absorbers. You'll find that they offer superior heat transfer properties, making them ideal for applications where rapid and uniform heat distribution is essential.
When you're considering aluminum nitride composites, you'll notice their remarkable resistance to thermal shock. This characteristic allows them to withstand sudden temperature changes without cracking or degrading. They're also known for their high temperature stability, maintaining their performance even in extreme heat conditions.
You'll appreciate the lightweight nature of these composites, which makes installation and handling easier compared to traditional materials. They're also corrosion-resistant, ensuring longevity in various environments. When you integrate aluminum nitride composites into your heat collector panels, you'll benefit from their ability to enhance overall system efficiency.
As you explore these materials, you'll discover that they can be tailored to specific requirements by adjusting their composition. This flexibility allows for optimized performance in different types of heat collection systems, making aluminum nitride composites a versatile choice for your energy-efficient projects.
Spectrally Selective Paint
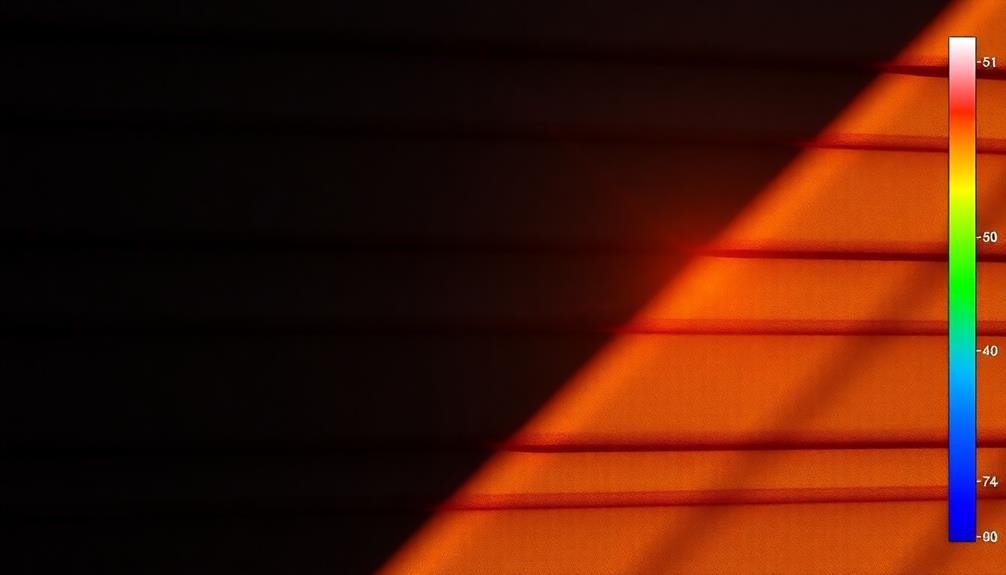
Spectrally selective paint revolutionizes the efficiency of heat collector panels. This innovative coating optimizes solar absorption while minimizing heat loss through radiation. You'll find that these paints are engineered to absorb a wide range of solar wavelengths but emit very little infrared radiation, resulting in higher thermal efficiency.
When you're considering spectrally selective paint for your heat collector panels, keep in mind its key advantages:
- High solar absorptance (typically >0.90)
- Low thermal emittance (usually <0.20)
- Durability in harsh environmental conditions
- Easy application on various substrates
You'll notice that these paints often contain pigments like black chrome, nickel, or titanium nitride. These materials create a selective surface that traps solar energy effectively.
As you apply the paint, you're fundamentally creating a multi-layered coating that acts as both an absorber and a reflector.
In practical terms, you'll see improved performance in your heat collector panels. The paint helps maintain higher temperatures, even in cooler ambient conditions. This translates to better overall system efficiency and potentially lower operating costs for your solar thermal applications.
Anodized Aluminum Surfaces
For heat collector panels, anodized aluminum surfaces offer an excellent alternative to paint-based coatings. You'll find that anodizing creates a durable, corrosion-resistant layer on aluminum substrates, enhancing their thermal absorption properties. This process involves electrochemically oxidizing the aluminum surface, resulting in a porous oxide layer that can be further treated to improve its optical characteristics.
When you're considering anodized aluminum for your heat collector panels, you'll appreciate its high absorption in the visible and near-infrared spectrum while maintaining low emissivity in the far-infrared range. This selective absorption profile maximizes solar energy capture and minimizes heat loss. You can further optimize the anodized surface by incorporating colored dyes or metal particles into the pores, fine-tuning its spectral selectivity.
Anodized aluminum surfaces boast excellent durability, often lasting longer than painted coatings. They're resistant to UV degradation and weathering, ensuring consistent performance over time. You'll also find that anodized surfaces are easier to clean and maintain, reducing operational costs.
When selecting anodized aluminum for your heat collector panels, consider factors like the anodizing thickness, pore size, and any additional treatments to achieve the desired thermal performance.
Polymer-Based Nanocomposites

Cutting-edge research in absorber materials has led to the development of polymer-based nanocomposites for heat collector panels.
These innovative materials combine polymer matrices with nanoscale fillers, offering unique properties that enhance thermal absorption and overall panel efficiency.
You'll find that polymer-based nanocomposites provide several advantages over traditional absorber materials, including lightweight construction, improved durability, and cost-effectiveness.
When considering polymer-based nanocomposites for your heat collector panels, keep in mind these key features:
- Tunable optical properties for optimized solar absorption
- Enhanced thermal conductivity for efficient heat transfer
- Improved mechanical strength and resistance to environmental factors
- Potential for large-scale, low-cost manufacturing processes
Frequently Asked Questions
How Do Environmental Factors Affect the Long-Term Performance of Absorber Materials?
Environmental factors greatly influence absorber materials' long-term performance. You'll find that UV radiation, temperature fluctuations, humidity, and air pollutants can degrade their efficiency over time. It's essential to take these factors into account when selecting and maintaining absorber materials.
What Are the Cost Considerations for Implementing Different Absorber Materials?
You'll find that costs vary widely for absorber materials. You're looking at factors like raw material prices, manufacturing processes, and installation complexity. Don't forget to take into account long-term savings from efficiency and durability when making your choice.
Can These Materials Be Recycled or Repurposed at the End of Their Lifecycle?
You'll be pleased to know that many absorber materials can be recycled or repurposed. You can often reclaim metals like copper and aluminum. Some polymers and composites are also recyclable. It's best to check with manufacturers for specific recycling options.
How Do Absorber Materials Impact the Overall Efficiency of Solar Thermal Systems?
Absorber materials greatly impact your solar thermal system's efficiency. They're essential in capturing and transferring heat. The better they absorb sunlight and conduct heat, the more energy you'll harness, boosting your system's overall performance.
Are There Any Health or Safety Concerns Associated With Manufacturing These Materials?
You'll find some health and safety concerns in manufacturing absorber materials. They often involve hazardous chemicals, toxic fumes, and high temperatures. You should always follow safety protocols and use proper protective equipment when working with these materials.
In Summary
You've explored a range of cutting-edge absorber materials for heat collector panels. From black chrome coatings to polymer-based nanocomposites, you've seen how innovation is driving solar thermal efficiency. As you consider these options, remember that each material offers unique benefits. Whether you're prioritizing cost, durability, or peak performance, there's likely a solution that fits your needs. Keep an eye on emerging technologies – they'll shape the future of solar thermal energy collection.
Leave a Reply