To keep your micro-hydro system running smoothly, you'll need to focus on regular maintenance. Clean intake screens frequently to prevent clogging, manage sediment buildup, and inspect turbine blades for wear. Monitor water flow rates consistently and perform electrical system checks to guarantee safety and efficiency. Don't forget to lubricate moving parts, waterproof critical components, and apply anti-corrosion coatings where needed. Pay attention to bearings and shaft alignment, and prepare your system for winter conditions. By following these practices, you'll maximize your system's performance and longevity. There's more to discover about maintaining your micro-hydro setup.
Regular Intake Screen Cleaning
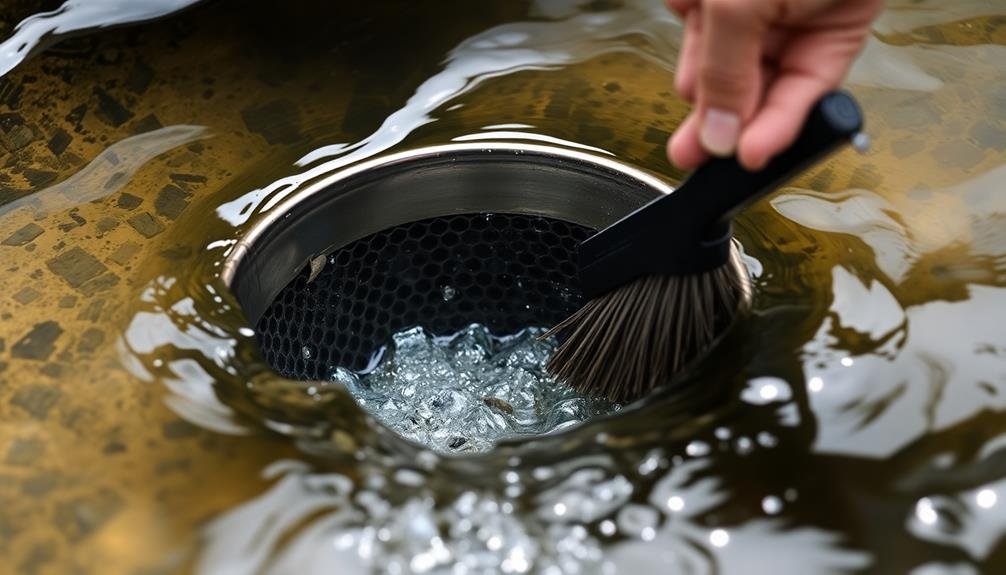
Debris can quickly clog your micro-hydro system's intake screen, reducing water flow and power generation. To prevent this, you'll need to clean the intake screen regularly. The frequency of cleaning depends on your water source's characteristics, but it's typically necessary every few days to weeks.
Start by shutting off the water flow to your system. Carefully remove the screen and inspect it for damage. Use a soft brush or low-pressure water spray to remove leaves, twigs, and sediment. For stubborn debris, gently scrape the screen with a plastic scraper. Avoid using metal tools that could damage the screen.
Check the screen for tears or holes and repair or replace it if necessary. Before reinstalling, examine the intake area for any accumulated debris and clear it out. Securely reattach the clean screen and restart your system.
Consider installing an automated screen cleaner for high-debris areas. These systems use water jets or mechanical brushes to keep the screen clear, reducing manual maintenance.
Additionally, implementing a debris diversion system upstream can greatly decrease the amount of material reaching your intake screen.
Proper Sediment Management
Vigilance is key when it comes to sediment management in your micro-hydro system. Regularly monitor and remove sediment buildup to prevent damage to your turbine and maintain ideal performance. Install a settling basin upstream of your intake to trap larger particles before they enter your system. You'll need to periodically clean this basin, especially after heavy rainfall or flooding events.
For finer sediment, consider implementing a flushing system. This allows you to periodically flush accumulated sediment from your pipeline without shutting down the entire system. Here's a quick guide to sediment management techniques:
Technique | Frequency | Benefits |
---|---|---|
Settling basin cleaning | Monthly | Prevents coarse sediment entry |
Pipeline flushing | Quarterly | Removes fine sediment buildup |
Turbine inspection | Annually | Identifies wear and damage |
Don't forget to inspect your turbine regularly for signs of erosion or wear caused by sediment. If you notice any issues, address them promptly to avoid more significant damage. By implementing these sediment management practices, you'll extend the life of your micro-hydro system and guarantee it continues to operate at peak efficiency.
Turbine Blade Inspection
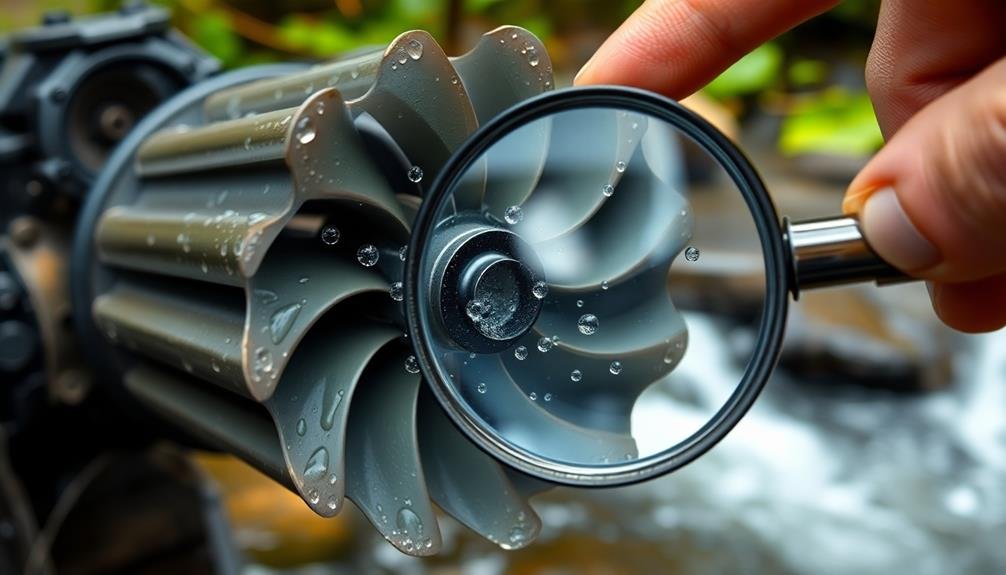
Check your turbine blades regularly for signs of wear and tear, including pitting, erosion, or cracks.
You'll need to clean the blade surfaces thoroughly to properly assess their condition.
Look for any buildup of debris, algae, or mineral deposits that could affect the turbine's efficiency.
Wear and Tear Signs
Regular inspection of turbine blades is essential for maintaining your micro-hydro system's efficiency and longevity.
As you examine the blades, look for signs of wear and tear that could impact performance. Pay close attention to the leading and trailing edges, where damage is most likely to occur.
Common wear and tear signs you should watch for include:
- Pitting or erosion on the blade surface
- Cracks or chips along the edges
- Deformation or bending of the blade shape
- Discoloration or corrosion
- Debris buildup or foreign objects stuck to the blades
If you notice any of these issues, take action promptly.
Minor damage can often be repaired, but severe wear may require blade replacement.
Don't ignore small problems, as they can quickly escalate and cause system-wide inefficiencies or failures.
Cleaning Blade Surfaces
Keeping your turbine blades clean is essential for maintaining ideal performance. Over time, debris, algae, and mineral deposits can accumulate on the blade surfaces, reducing efficiency and potentially causing imbalances. You'll need to inspect and clean your turbine blades regularly to prevent these issues.
Start by shutting down your system and draining the turbine housing. Once it's safe to access, visually examine the blades for any buildup or damage. Use a soft brush or cloth to gently remove loose debris.
For tougher deposits, you may need to use a mild detergent solution or specialized cleaning products designed for hydro turbines. Be careful not to scratch or damage the blade surfaces while cleaning. If you encounter stubborn mineral deposits, you might need to use a weak acid solution, but always follow the manufacturer's guidelines.
After cleaning, rinse the blades thoroughly with clean water to remove any residual cleaning agents. Before restarting your system, verify all blades are clean and free from obstructions.
Regular cleaning will help maintain your turbine's efficiency, extend its lifespan, and prevent costly repairs down the line.
Monitoring Water Flow Rates
To guarantee ideal performance of your micro-hydro system, monitoring water flow rates is essential. Regular checks ascertain your system operates at peak efficiency and helps you detect potential issues early.
You'll need to measure the flow rate at various points in your system, including the intake, penstock, and turbine output. Use a flow meter or other appropriate measuring devices to track water flow. Keep a log of your measurements, noting any notable changes or patterns.
This data will help you:
- Identify seasonal fluctuations in water availability
- Detect leaks or blockages in the system
- Optimize turbine performance
- Plan for maintenance or upgrades
- Estimate power output accurately
Pay close attention to sudden drops in flow rate, as they may indicate problems like debris buildup or pipe damage. If you notice a consistent decline in flow over time, it could signal issues with your water source or intake structure.
Don't forget to check your system's flow rate after heavy rains or during dry spells, as these events can notably impact performance.
Electrical System Checks
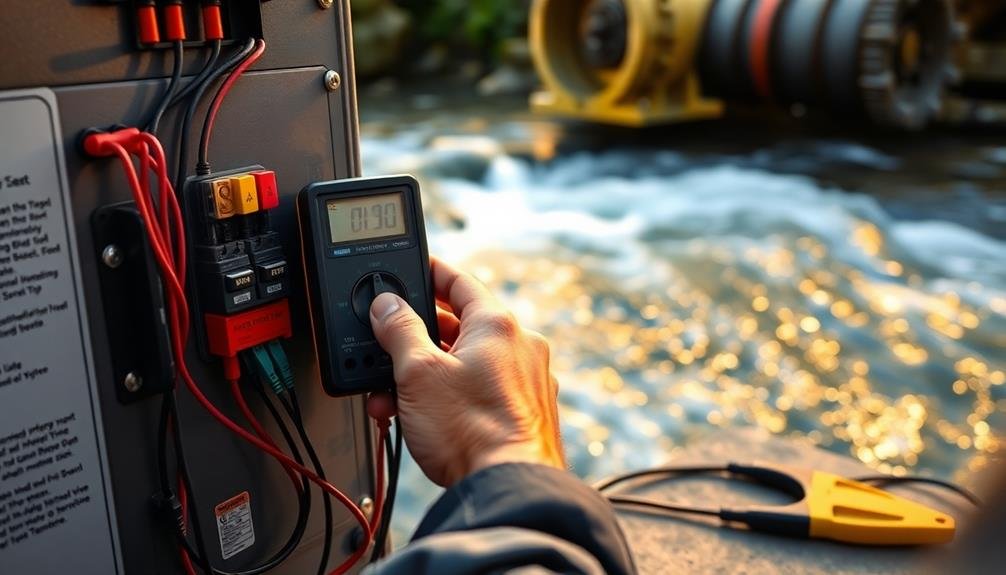
Electrical system safety is vital when maintaining your micro-hydro setup. You'll need to regularly inspect and test various components to guarantee your system operates efficiently and safely.
Start by checking all electrical connections for tightness and signs of corrosion. Loose connections can cause voltage drops and overheating, while corrosion can lead to increased resistance and reduced efficiency.
Next, examine the generator's brushes and commutator. Look for excessive wear on the brushes and smooth, even wear on the commutator. Replace brushes that are worn down to less than half their original length.
Inspect the insulation on all wiring for cracks, fraying, or other damage that could lead to short circuits.
Don't forget to test your system's grounding. Proper grounding is essential for safety and protection against lightning strikes. Use a multimeter to verify the resistance between the ground rod and neutral connections.
It's also important to check your charge controller and inverter settings to guarantee they're optimized for your system's current output and battery bank.
Lastly, review your battery bank's performance. Check individual cell voltages, electrolyte levels in flooded batteries, and overall battery capacity.
Clean battery terminals and apply anti-corrosion coating to prevent buildup.
Lubrication of Moving Parts
Proper lubrication of moving parts is essential for your micro-hydro system's longevity and efficiency. You'll need to regularly inspect and lubricate components like turbine bearings, generator bearings, and any gears or pulleys in your system. This prevents excessive wear, reduces friction, and helps maintain peak performance.
When lubricating your system, consider these key points:
- Use the correct type of lubricant for each component
- Follow the manufacturer's recommendations for lubrication intervals
- Clean parts thoroughly before applying new lubricant
- Check for signs of wear or damage during lubrication
- Keep detailed records of your maintenance activities
You'll want to pay special attention to water-exposed components, as they're more prone to corrosion and wear. Use water-resistant lubricants where appropriate, and guarantee proper sealing to prevent water ingress.
Don't forget to lubricate less obvious parts like control valves and intake screens.
Regularly scheduled lubrication will help you catch potential issues early, saving you time and money on repairs.
It'll also keep your system running smoothly, maximizing power output and extending its lifespan.
Waterproofing and Corrosion Prevention
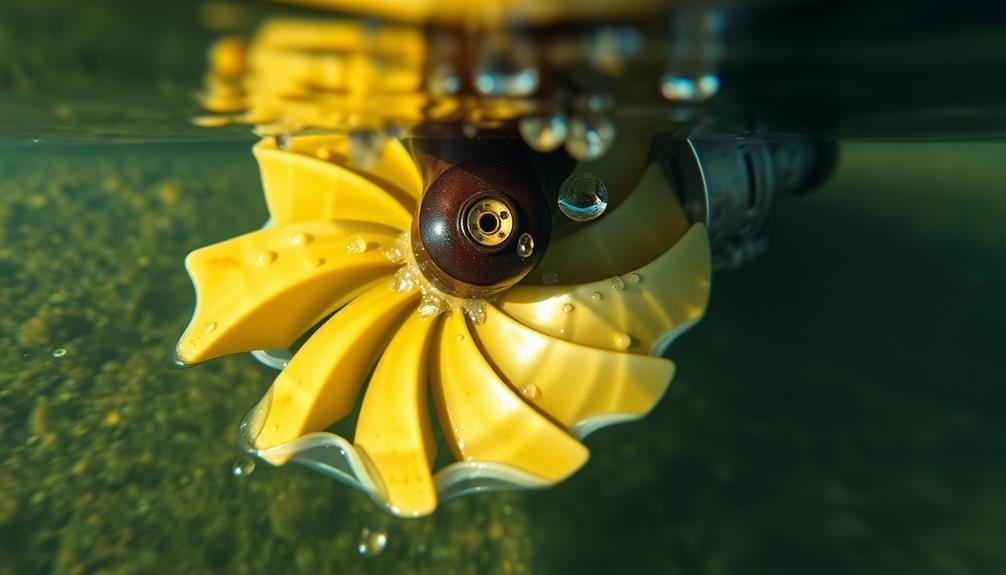
To protect your micro-hydro system from water damage and corrosion, you'll need to focus on two key areas.
First, guarantee you're properly sealing all critical components, including electrical connections and sensitive equipment housings.
Next, apply anti-corrosion coatings to exposed metal surfaces, paying special attention to turbine parts and structural elements that come into direct contact with water.
Sealing Critical Components
Sealing critical components is an essential aspect of micro-hydro system maintenance. You'll need to guarantee that all vulnerable parts are properly protected from water ingress and corrosion. Focus on sealing the generator, electrical connections, and control panels to prevent moisture-related damage and extend your system's lifespan.
When sealing components, consider using:
- Silicone-based sealants for flexible, waterproof joints
- Epoxy resins for strong, permanent seals
- Rubber gaskets for removable access points
- Waterproof tape for temporary or emergency fixes
- Specialized coatings for metal surfaces prone to corrosion
Apply sealants carefully, guaranteeing complete coverage without interfering with moving parts. Pay special attention to cable entry points, junction boxes, and areas where different materials meet.
Don't forget to seal any conduits or pipes that carry wires or water, as these can be common entry points for moisture.
Regularly inspect your seals for signs of wear or damage. Replace them promptly if you notice any deterioration.
Anti-Corrosion Coatings Application
Applying anti-corrosion coatings is crucial for protecting your micro-hydro system against the constant onslaught of water and environmental factors.
You'll need to choose the right coating for your system's materials and operating conditions. Epoxy-based coatings are popular for their durability and excellent adhesion to metal surfaces. For underwater components, you'll want to use a marine-grade coating that can withstand constant submersion.
Before applying the coating, thoroughly clean and prepare the surfaces. Remove any rust, dirt, or old paint using wire brushes, sandblasting, or chemical cleaners.
Apply the coating in thin, even layers, following the manufacturer's instructions for drying times and recoat intervals. Pay special attention to edges, corners, and joints where corrosion often begins.
Don't forget to coat both the interior and exterior of pipes, turbines, and other water-contacting components. For ideal protection, apply multiple layers, allowing each to dry completely before adding the next.
Regularly inspect your coatings for signs of wear or damage, and touch up as needed to maintain a continuous protective barrier.
Bearings and Shaft Alignment
Maintaining proper bearing condition and shaft alignment is vital for the efficient operation of a micro-hydro system. You'll need to regularly inspect and lubricate bearings to prevent wear and reduce friction.
Misaligned shafts can cause excessive vibration, leading to premature component failure and reduced system efficiency.
To guarantee peak performance, you should:
- Check bearing temperature during operation
- Listen for unusual noises or vibrations
- Inspect seals for signs of leakage
- Measure shaft runout with a dial indicator
- Use laser alignment tools for precision adjustments
When performing maintenance, clean bearings thoroughly and replace them if you notice any signs of damage or excessive wear.
It's essential to use the correct type and amount of lubricant as specified by the manufacturer.
For shaft alignment, start by checking coupling alignment and adjust as needed.
Remember that even small misalignments can greatly impact system efficiency and component lifespan.
Winter Preparation and Maintenance
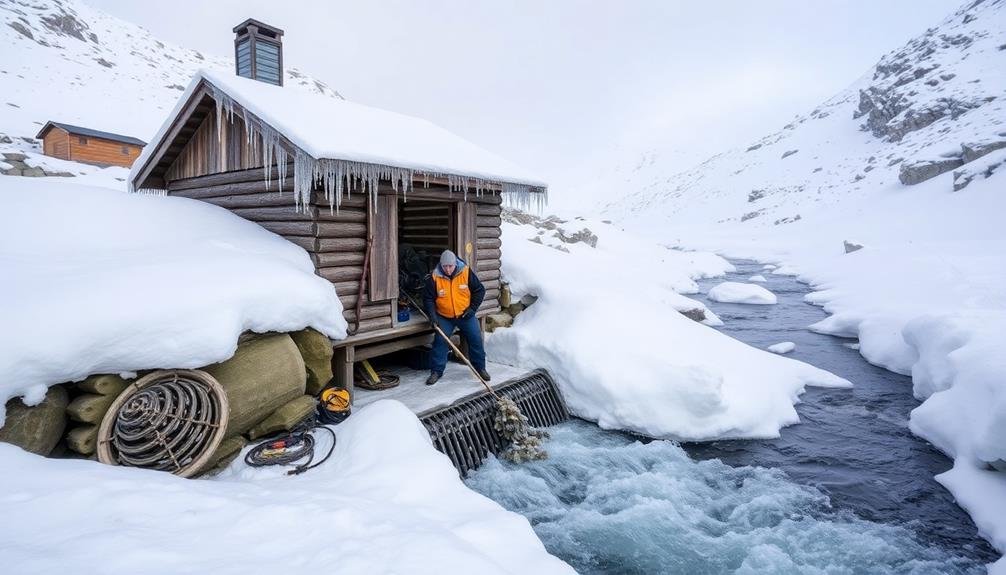
With the change of seasons, your micro-hydro system faces new challenges. As winter approaches, you'll need to take specific steps to protect your equipment and guarantee continuous operation.
Start by inspecting your intake screen and removing any accumulated debris. Install a de-icing system or heat tape around vulnerable components to prevent freezing.
Check your penstock for leaks or weak spots, as freezing water can cause significant damage. Insulate exposed pipes and consider burying them deeper if possible. Drain any components that aren't in use to prevent ice formation.
Adjust your system's flow rate to accommodate changes in water levels due to ice buildup or reduced stream flow.
Regularly monitor your battery bank's performance in colder temperatures, as capacity can decrease. Keep snow and ice away from solar panels if you're using a hybrid system.
Lubricate moving parts with cold-weather-specific grease to maintain smooth operation. Install a remote monitoring system to alert you of any issues, especially if your site is difficult to access during winter months.
Frequently Asked Questions
How Long Does a Typical Micro-Hydro System Last?
Your micro-hydro system can last 20-30 years with proper maintenance. You'll need to regularly inspect and clean components, replace worn parts, and guarantee water quality. Don't forget to monitor performance and address issues promptly for longevity.
Can Fish Pass Safely Through a Micro-Hydro Turbine?
You shouldn't expect fish to safely pass through a micro-hydro turbine. It's best to install fish-friendly screens or bypass systems to protect aquatic life. These measures guarantee your system doesn't harm the local ecosystem while generating power.
What's the Average Payback Period for a Residential Micro-Hydro Installation?
You'll typically see a payback period of 5-10 years for residential micro-hydro systems. It depends on your site's potential, electricity rates, and installation costs. With proper maintenance, you'll enjoy free, clean energy for decades after.
Are There Any Government Incentives for Installing Micro-Hydro Systems?
Yes, you'll find various government incentives for micro-hydro installations. You can benefit from federal tax credits, grants, and rebates. Check your state's energy office for local incentives, as they vary by location and system size.
How Noisy Are Micro-Hydro Systems Compared to Other Renewable Energy Sources?
You'll find micro-hydro systems are relatively quiet compared to other renewables. They produce a low hum from the turbine, which is often muffled by flowing water. Wind turbines and some solar inverters can be noisier.
In Summary
You've learned the key elements to keep your micro-hydro system running smoothly. By regularly cleaning intake screens, managing sediment, inspecting turbines, monitoring flow rates, and checking electrical systems, you'll maintain peak performance. Don't forget to lubricate moving parts, prevent corrosion, align bearings and shafts, and prepare for winter. With consistent care and attention to these details, you'll guarantee your system continues to generate clean, reliable energy for years to come.
Leave a Reply